Tasline is made from Ultra high molecular weight polyethylene (UHMWPE) which has the highest impact strength of any thermoplastic presently made.
In simplified terms, the yarn starts its life by being spun and the centrifugal force pushes the polyethylene through microscopic holes. This sounds simple enough but just imagine, the 50lb 8 strand line may be made out of 8 strands of 100 denier yarn. Each of those 100 denier strands is actually made from a filament that has 50 individual micro strands if the filament dtex is 2.0. So a 50lb line would be made from 400 individual micro strands!! And some yarns have an even lower dtex, so it’s even finer.
These individual strands are so thin that it is not possible to braid them in a braiding machine. Therefore, the first process is to twist these yarns with up to 100 twists per meter, depending on the size of the yarn.
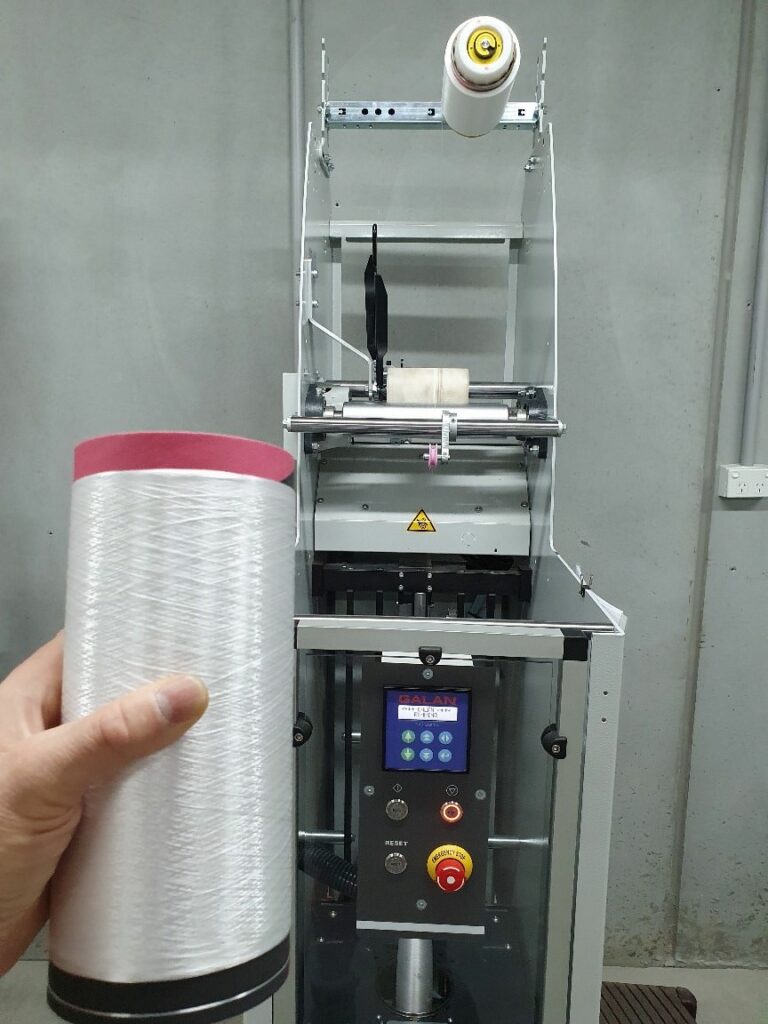
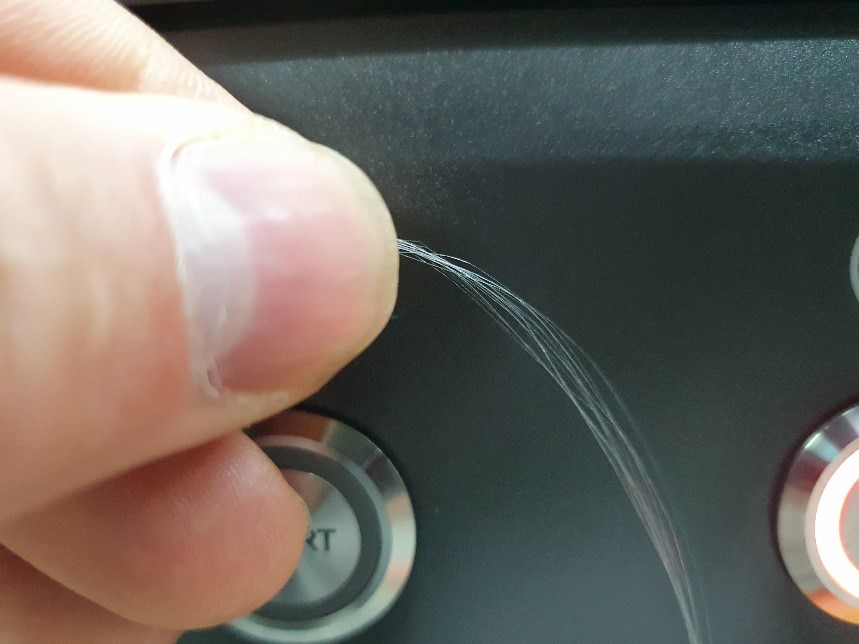
The yarn is fed from the top under a rubber roller and down onto the spindle. The spindle and a small clip, which is called the traveller, spins at up to 6000rpm and the traveller provides the tension by centrifugal force. The traveller rotates on a ring which is programmed to go up and down the spindle in a certain pattern, to create what’s known as a bottle of twisted yarn.
Depending on rotation this will give what’s known as a S or a Z twist.
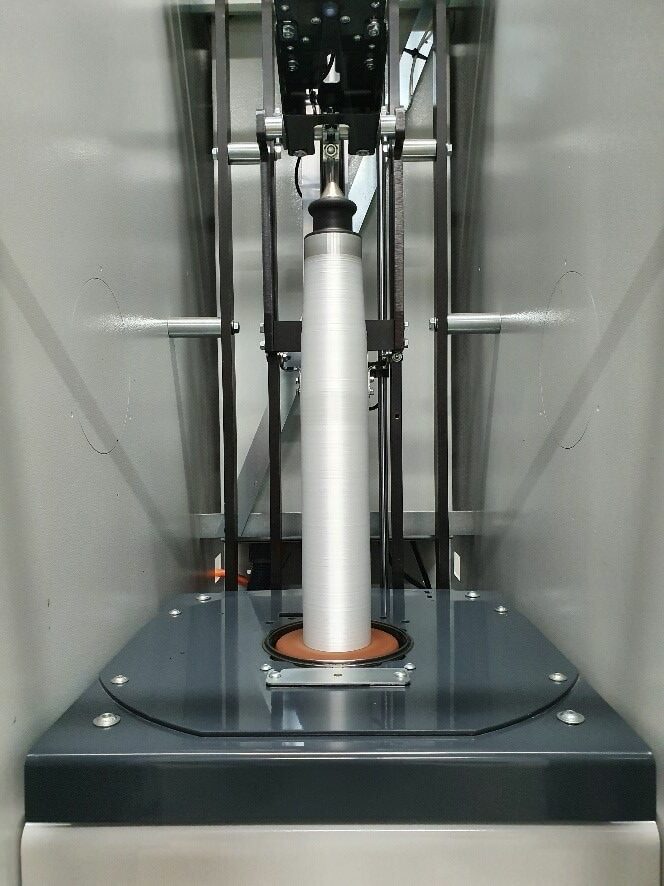
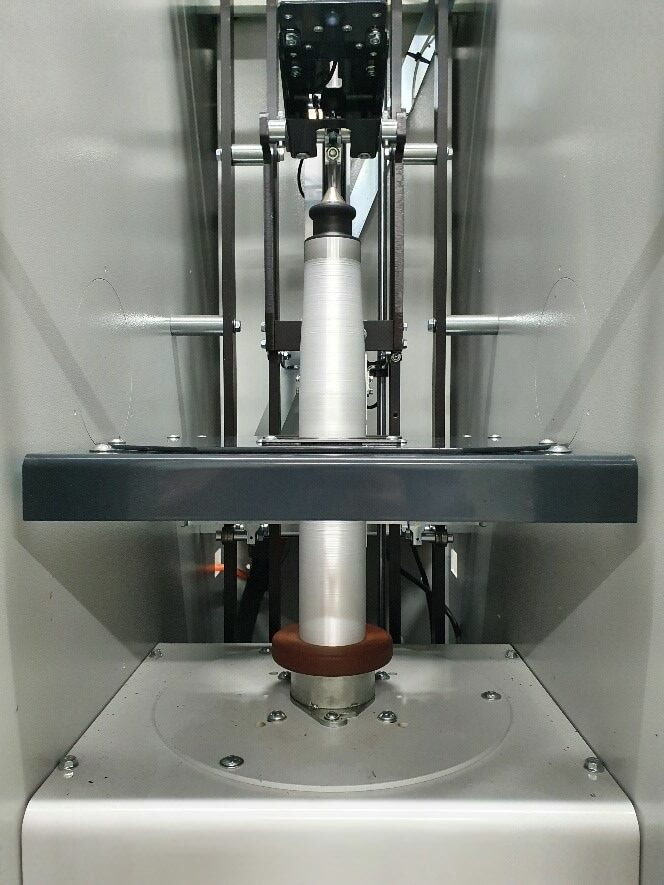
This process is called “ring twisting” and the twisting machines at Tasline are from Galan in Spain.
The next process is perhaps the most important. The twisted yarn is now wound onto bobbins that go into the braiding machines later. Tasline uses the latest technology from Herzog in Germany, as it’s critical to apply the correct tension 100% of the time, as otherwise the yarn could be damaged. Therefore, this winder has electronic tensioning controls and is fully automatic.
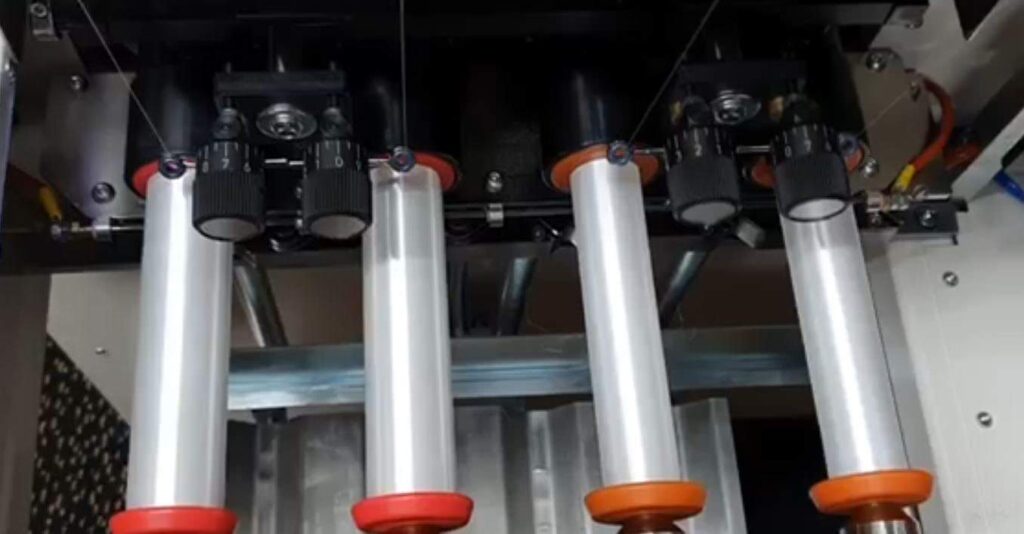
4 bobbins at a time are automatically loaded and the twisted yarn is then spooled onto the bobbins to perfection.
The spooled bobbins are then loaded into the braiding machines. These machines have 8 carriers per head. This means that 8 bobbins will fit onto the carriers to make 8 strand braid. These carriers then rotate in a figure 8 pattern at high speed to funnel the twisted yarns up to the braiding point where it is braided together and pulled up to the take up spool.
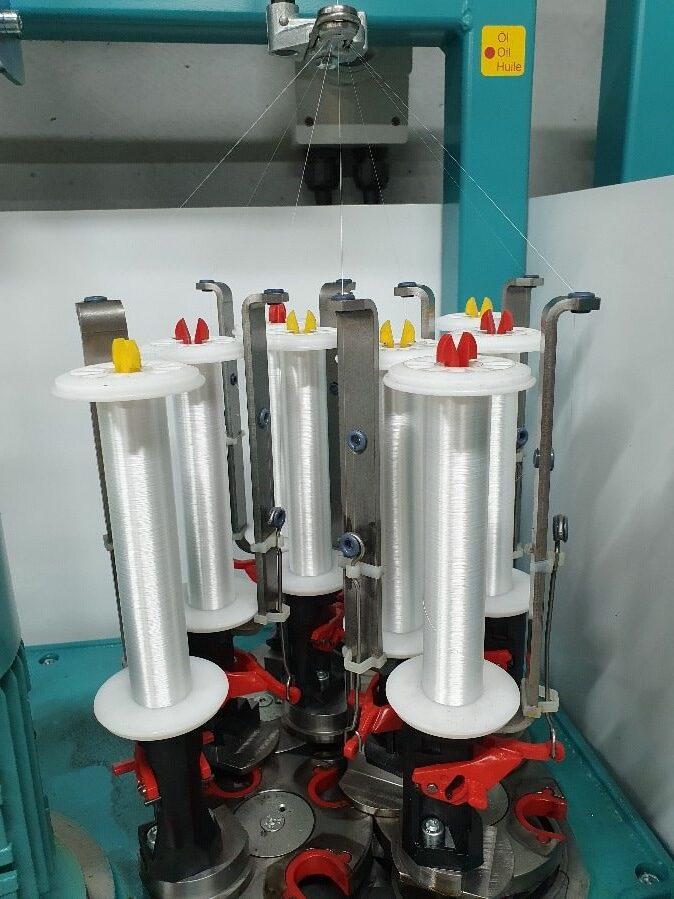
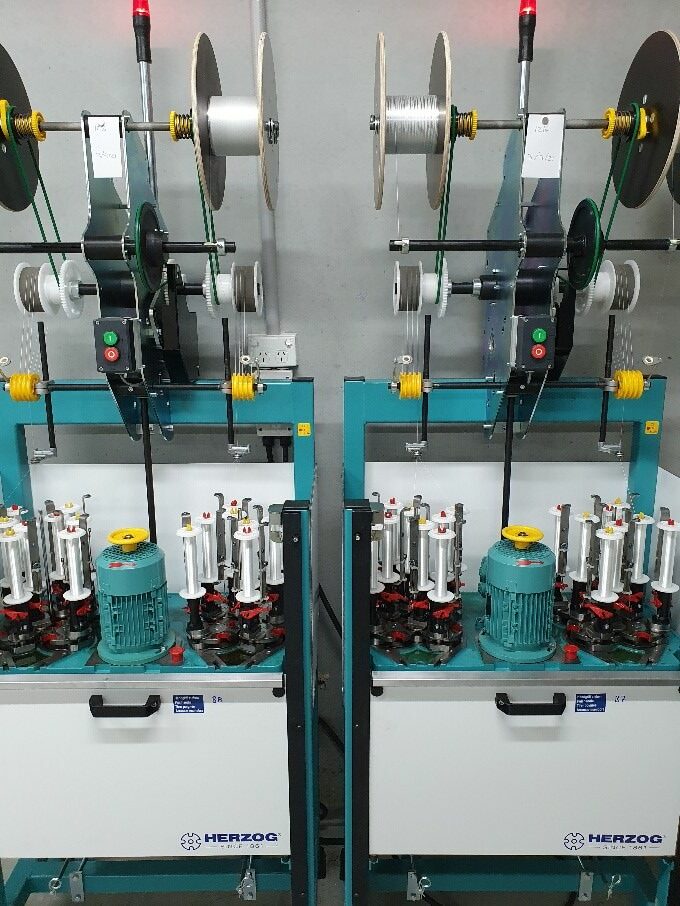
Although the carriers run very fast, making braid is very slow. For example, it takes over 3 days to make 1000m of 16lb Tasline on one head. Typically, there are up to 5000 meters in a batch and depending on which pound line is getting braided, these machines will run for up to 12 days without stopping. Once one of the bobbins runs out of yarn, the braiding machine will stop.
The finished line is then taken off the braider and transferred to another process, which unfortunately can’t be shown. Some manufacturers use a heat stretching process, where the lines are stretched in an oven under heat and some manufacturers also use dies and coatings. Tasline has a proprietary process without any coatings, which leaves it smooth and supple, while maintaining high wear resistance and strength.
The final process is the testing of every spool that comes off the braiding machines. Since the start of 2021, each spool has a #number written on the back of the spool and the test results are recorded publicly. For the results and how the testing is done, please see our Tasline testing blog.
Also please check out some great footage in our video “How Tasline braid is made”
Thanks for your support from the Tasline team!